Warehouse Assessment & Operations Assessment
Every business continually feels the pressure to reduce warehouse and distribution costs and improve customer service. With labor becoming more expensive and harder to find, now more than ever is the time to evaluate the operations and determine ways to be more efficient and reduce costs.
To improve the operations, companies must constantly assess and refocus improvement efforts in all areas of their distribution center and warehouse operations. This is where a warehouse assessment, or operations assessment, comes into play.
An operations assessment is a comprehensive evaluation and analysis of all functions, departments, and aspects within your operation, including:
- All processes from receiving through shipping and returns processing.
- Inventory management practices within the operations including cycle counting, physical inventories and bin management.
- All material handling equipment, storage, and automation within the facility.
- The overall flow of goods and people through the facility from one department to another.
- The warehouse management systems that control all inventory functions, Value Added Services (VAS) and order fulfillment functions.
- The organizational structure and support of the operations from management through the supervisors and leads by department.

We assist our clients by conducting an objective, independent operations assessment to identify all areas for potential improvement. We collaborate with our clients to develop well-focused actionable, detailed recommendations that implement industry best practices.
An operations assessment is conducted, utilizing our industry expertise, along with in-depth interviews of key staff throughout your operations.
These interviews allow us to better understand the current processes and issues being faced, which are then combined with our observations during the site visit. In addition, these interviews allow us to understand your company culture, product mix, order profiles, and warehouse management system that support the operations.
We draw upon our years of knowledge and expertise derived from performing hundreds of facility assessments to provide recommendations that have a proven track record of improving operations.
These recommendations can be immediately implemented into your current distribution center or used in planning and opening a future distribution center. Our recommendations will boost worker productivity, increase efficiencies, and improve product workflow in your distribution center; all which will reduce your overall warehouse expenses and cost.
Operations Assessment Objectives
Receiving and Putaway
- Short-term and long-term process recommendations to improve throughput and efficiency, including what changes are needed to support the anticipated growth of inbound goods.
- Recommended layout changes to facilitate receiving processes, inbound staging, and staging for putaway.
- A rough understanding of how long the recommended process or layout changes would take to implement.
- Feedback and recommendations related to vendor compliance on inbound goods.
- Identification of potential system gaps that create inefficiencies in receiving and putaway.
- Recommendations regarding the labor (hourly and supervisory) that would assist with improving receiving and putaway.
- Feedback and recommendation on whether potential automation should be considered to support the receiving and putaway process.

Picking and Replenishments
- Short-term and long-term process recommendations to improve throughput and efficiency, including what changes are needed to support the anticipated growth in order volume.
- Recommended layout changes to facilitate efficient picking and flow of goods through to packing.
- A rough understanding of how long the recommended process or layout changes would take to implement.
- Feedback and recommendations on changes to picking methods to support the increased volumes.
- Identification of potential system gaps that create inefficiencies in the picking process.
- Recommendations regarding the labor (hourly and supervisory) that would assist with improving the picking process and efficiency.
- Feedback and recommendations regarding the replenishment process and ways to minimize labor, and the frequency of replenishments.
- Feedback and recommendation on whether potential automation should be considered to support the picking process.
Packing and Shipping
- Short-term and long-term process recommendations to improve throughput and efficiency, including what changes are needed to support the anticipated growth in package volume.
- Recommended layout changes to facilitate efficient packing and manifesting of orders – as well as the staging or loading of outbound orders.
- A rough understanding of how long the recommended process or layout changes would take to implement.
- Feedback and recommendations on changes to the packing of orders, and the manifesting of outbound cartons.
- Identification of potential system gaps that create inefficiencies in the packing and shipping processes.
- Recommendations regarding the labor (hourly and supervisory) that would assist with improving the packing process and efficiency.
- Feedback and recommendation on whether potential automation should be considered to support the packing, manifesting, and shipping processes.
Returns Management
- Short-term and long-term process recommendations to improve throughput and efficiency, including what changes are needed to support the anticipated growth in return package volume.
- Recommended layout changes to facilitate efficient processing of customer orders, including efficient removal of waste and recycling and staging of goods to be returned to stock.
- Feedback and recommendations on changes to the packing of orders, and the manifesting of outbound cartons.
- A rough understanding of how long the recommended process or layout changes would take to implement.
- Identification of potential system gaps that create inefficiencies in processing customer returns and dispositioning inventory.
- Recommendations regarding the labor (hourly and supervisory) that would assist with improving the returns process.
Inventory Control & Bin Management
- Feedback and recommendations on how cycle counting, and physical inventories are being performed.
- Feedback and recommendations regarding how product is current being slotted, and what changes should be made to gain efficiencies in stock putaway, picking and replenishments.
- Feedback and recommendations regarding the days of supply on hand in the pick slots to gain efficiencies and reduce the impacts on labor.
- A rough understanding of how long the recommended process or layout changes would take to implement.
- Feedback and recommendations to the use of warehouse zones to support the operations.
- Feedback and recommendations regarding the location schema and labelling of bin locations.
- Identification of potential system gaps that create inefficiencies in managing the SKUs, the physical inventory and stock locations.
- Recommendations regarding the labor (hourly and supervisory) associated with inventory control and management, as well as bin management.

Benchmarking, Productivity and KPI’s
- Feedback and recommendations on productivity reporting and tracking for hourly labor.
- Feedback and recommendations on major KPIs and metrics that should be analyzed and managed on a regular basis, including areas such as:
- Cost per order fulfilled.
- Cost per order returned.
- Aged inventory, inventory turns and carrying costs.
- Feedback and recommendations for implementing productivity tracking, benchmarking and KPI reporting.
- A rough understanding of how long the recommended process changes would take to implement.
Additional Areas of Focus in an Operations Assessment
- Estimates for any material handling and equipment recommendations, including the lead times and vendors to purchase from.
- An understanding of how long the recommendations would take to fully implement.
- Estimates for any software recommendations, including the lead times and vendors to purchase from.
- An understanding of how long the recommendations would take to fully implement.
- Feedback on how all the process and layout changes would impact overall capacity and utilization of the facility.
- High-level, overall understanding of how well the system supports the overall business, and its ability to support the future SKUs and growth.
- Feedback and recommendations for any safety concerns related to the current facility and operations.
All recommendations from operations assessments are delivered back to you in a detailed, actionable report that will be your roadmap for immediately taking action in your operations.
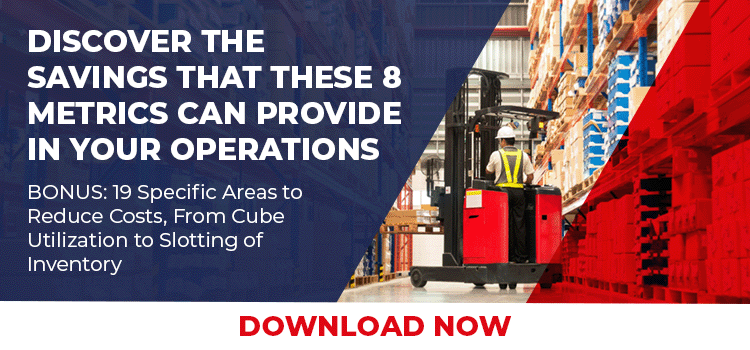