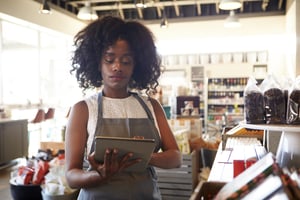
Over the years, many facets have changed within supply chains and distribution center operations. Wages and consumer demand have increased dramatically, however, the availability of quality labor to meet the order volumes and customer expectations are less than desirable.
It is imperative in today’s evolving supply chain environment to become more efficient and productive while making every effort to reduce labor and operational costs. There are many ways to go about this arduous task, but one of the first and most practical steps is to perform a warehouse assessment.
A Fulfillment Center Operations Assessment
A warehouse operations assessment, or audit, takes a quantitative and qualitative look at your distribution center operation in a systematic and disciplined way. As part of our distribution consulting services, we assist clients with performing these detailed operational assessments. This article shares our thoughts and insights on why every fulfillment company should perform operational assessments.
The results of these operational assessments will allow you to achieve better throughput, more efficient ways to store inventory, reduce costs, increase productivity, and improve customer satisfaction.
As you perform a warehouse assessment or audit, below are 9 benefits of performing an operational assessment.
Reduce Freight Costs and Improve Time in Transit
Outbound freight costs, whether small parcel or LTL, is typically one of the costliest budget items in a distribution center. In addition, the time in transit certainly plays a role in customer satisfaction. Understanding the profile of all your shipments is critical to reducing transportation costs. An operations assessment should include an analysis of the outbound freight to learn more, including:
- The type of freight being sent and are there opportunities to utilize lower-cost freight options without sacrificing time in transit.
- How many split shipments are occurring and why? Identify what is causing these split shipments and look for opportunities to reduce them. Are there inventory issues or backorders causing problems, are there packaging opportunities to minimize the number of split shipments?
- How well have your freight contracts been negotiated? Have you utilized an outside objective third party to determine if there is an additional opportunity? How much could regional carriers save on freight costs while providing significant decreases in time in transit?
Reduce Operational Costs by Implementing Vendor Compliance
Everything starts at your warehouse's receiving door. Moreover, every function, from put-away to shipping orders, is impacted in some way by your vendors in terms of cost, rework, and inability to use inventory immediately.
Operational assessments typically point to areas in the processes where companies should develop and enforce a vendor compliance program. Vendor compliance programs need to define and detail the expectations and specifications required of every vendor. The program also should include corrective processes to be used and ramifications for non-compliance.
Typically, vendor compliance programs seek to address a variety of processes, including:
Labeling of products with barcodes and other retail-ready tags that are required.
- Labeling of inbound cartons with PO and SKU data.
- Specify exactly how inbound freight is to be shipped and which carrier accounts are to be utilized.
- For mixed SKU cases and pallets, it defines how these shipments are to be packaged.
Packaging for inbound goods including any poly bag requirements or retail-ready packaging. - A vendor compliance program will also identify any chargebacks and processes for non-compliance.
Improve the Available Space Utilization
Total occupancy costs (facility costs, taxes, insurance, maintenance, and utilities), as well as relocation costs, are higher than ever before. It’s imperative to maximize the available warehouse space in the current operations to avoid relocating if possible. An operations assessment should identify opportunities for maximizing the total square feet and the vertical height as well.
The assessment will help answer the following:
- Does it make sense to add additional, or different racking in certain areas of your distribution center?
- Is there wasted overhead space that should be recaptured?
- When you look up in the existing racking, is there “honeycombing” of space?
- Is your warehouse management system aiding in performing consolidation routines to free up space?
Improving Distribution Center Slotting
Processing customer orders is a major labor expense in warehousing and distribution. As much as 70 percent of a picker's time can be spent in “travel”, walking between locations. With high volume order days, even a small amount of saved travel time can add up.
An operations assessment will identify opportunities in slotting, including whether it’s time to consider a new slotting routine. Proper slotting can dramatically reduce the travel time. Be sure to account for product velocity, size, and weight of the product, as well as the size of the pick slot.
Try to store a minimum of 3-5 days of supply, or more, in the pick slots to eliminate constant replenishment. Do certain product families or items always sell together? These should be slotted in close proximity. For many the 80/20 rule holds true - maybe a hot pick zone makes sense to truly minimize travel time in your operations.
Remaining Clean and Organized
Generally, you can tell a lot about an organization and the type of culture just by inspecting the facility's overall organization and appearance. When assessing the operations, identify if there are areas where the operations could be better organized and cleaner, ownership does not want to feel as if their investments are being wasted.
Are the aisles and dock free of trash or clutter? What is the condition of all storage and material handling equipment? What are the employee bathrooms and breakrooms like? The answers to these questions can help or hurt culture and employee morale.
Warehouse Management Systems
One of the most important aspects of an operational assessment is identifying one of the following:
- Is it time to invest in a warehouse management system?
- Have I outgrown my current warehouse management system?
- Could the operations better utilize the existing warehouse management system?
To maximize the facility and labor in your operations, a warehouse management system is critical to controlling costs and meeting customer expectations. From inbound receiving and picking to inventory management, a WMS will create efficiencies and drive accuracy.
The assessment should help to answer the following questions from a systems perspective:
- Is the current system sufficient to meet the current inventory and customer demands?
- Can the system support our future growth?
- Are there processes that are not supported that are costing additional labor or negatively impacting customers?
- Are there modules that could be purchased that would make the current system more effective?
- Do you know if you are truly using the system the way it was designed, or using the system correctly?
- Are there aspects that should be changed, or reimplemented, to make better use of the current system?
Improving Performance Metrics
The old saying, “You can't improve what you don't measure”, holds true for improving labor efficiency. The simple process of measuring operating metrics and reporting the results to your employees will result in an improvement even if you do nothing else with the data. By setting expectations and then telling everyone how they're measuring up, you can improve overall productivity.
Set up productivity measurements in units and costs for all warehouse departments (e.g., receiving, stocking, replenishment). Reach out to others in the industry to benchmark yourself against your peers and look for areas to improve in. These are all opportunities that should be identified in an operational assessment.
Continual Process Improvement
A big part of warehousing and distribution efficiency lies within the processes. Every function should have a standard operating procedure and should be continually reviewed. Every step performed in the warehouse should be evaluated. Inbound, putaway, replenishment, picking, packing, inventory control, etc. During your operational assessment, carefully evaluate what can and should be tweaked to improve labor utilization and efficiencies.
Utilize and adjust min/max levels and pick location sizes to reduce the number of replenishments. Should picking change to cart bin batch picking or zone picking? Should order wave times and batching logic be edited? Ensure to evaluate the flow of people and goods with these processes. Does it make sense to reroute or move facets of the process to create efficiencies in flow?
Utilizing Third Party Logistics
It is not uncommon for an assessment to identify where certain functions can be outsourced. Outsourcing can allow you to offload bulk storage, kitting or light assembly, order fulfillment or even returns management. Regardless, these options allow your operations to recapture space and better utilize labor, while leveraging a third party to assist with augmenting your supply chain. Businesses are moving away from the labor headache and fulfillment and focusing on marketing and product development. Evaluate whether the outcome of your audit is worth executing and fixing, or if a 3PL makes sense for you.
Conclusion
A methodical, disciplined process will ensure that you identify areas of opportunity. It’s important to also generate a roadmap for moving forward and implementing the recommendations that are generated. Over time, be sure to take a checkpoint as part of your on-going operational improvement process to ensure you are still on track.
*Note: this post was originally published in 2011. We've updated it with recent industry information and republished it so you can get the same relevant information in its most accurate format.
SHARE