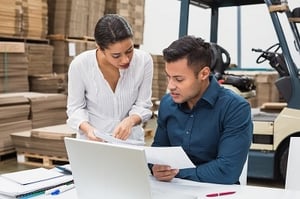
As part of our distribution consulting services, we have performed hundreds of operational assessments and identified several ways companies can save money through improved order processing and inventory storage. We have compiled the following quick-hitting list to be included in your warehouse assessment that will assist in reducing your supply chain operating expenses and improving customer satisfaction.
Reducing Labor Costs in Receiving, Putaway and Replenishments
-
Receive ASNs for inbound goods and begin scheduling dock times for receiving. An ASN can be as simple as an email stating that a PO is on its way from an inbound vendor, etc. This, along with scheduling dock times, will allow your operations to better plan labor around what needs to be processed, and if there is any critical inventory tied to backorders, etc., which will allow for prioritizing the workload.
-
Utilize directed putaway for more efficient putaway from receiving. Directed putaway keeps certain items in a home location or zone and keeps workers from searching for an open location that is suitable for the inventory.
-
Utilize technology such as mobile workstations, or handheld scanners with hip printers. We have all seen receiving departments where the computers, or label printers, are located at the far end of a dock. Workers spend a fair amount of time walking back and forth to look up items, print receivers, or generate the necessary warehouse or barcode labels. This type of technology keeps the workers productive and efficient.
-
When pulling replenishments, it is not uncommon for some operations to pull one or two items at a time and stage them for replenishment. Switch to batch pulling of the required inventory, utilizing your warehouse management system to assist with logically moving through the warehouse and building a pallet of inventory to be staged for replenishment of the pick slots.
Reducing Labor Costs in Picking, Packing, And Shipping
-
Consider various batching logic to make high volume order processing more efficient. It is imperative to separate out the single-line single unit and single-line multi-unit orders into their own batches and processes. These are the most efficient batches and can be handled most efficiently.
-
Evaluate the effectiveness of different picking methodologies for your operations such as zone-based batch picking or a zone-based pick and pass option. Both can increase the pick rates and overall throughput of your picking operations. In batch picking units, you will need to sort down to the order level using put walls or unit level sorters. Both options will also reduce labor costs.
-
Consider implementing goods-to-person technology from vertical lift modules, shuttle systems, or even Autonomous Mobile Robots (AMR). All these options keep the pickers in a very small footprint, with the ability to hit 400+ units per man-hour depending on the item characteristics, etc.
-
Consider picking directly to the shipping carton as opposed to sending all the orders to the pack stations. This reduces an additional touch point and speeds up throughput. When this is combined with automated dunnage, large portions of orders can bypass packing altogether – especially with the use of carton sealing.
-
If using pick carts, ensure that the pick carts are the right size to maximize order batches. It's not uncommon for companies to utilize a pick cart that holds 4 to 6 orders when they could utilize a larger cart to hold 10 to 12 orders. This would reduce the number of steps to be taken and the number of trips through the pick path. Also consider using different pick carts based on the size of the order, it's okay to utilize different-sized carts in a single operation.
-
Labor used to ship orders can be eliminated by utilizing automated print and applying equipment on the shipping line. Package weights and dimensions can be automatically captured, rate shopped, and a shipping label applied without human intervention.
-
Ensure pack stations can support at least 4 to 6 hours of packing supplies to keep workers from constantly leaving the pack stations. Companies can creatively solve the space challenges tied to the packaging supplies and look at shared supplies among packers. You may find that you have way more box sizes than what is necessary or feasible.
Additional Ways To Reduce Fulfillment Costs
-
Reduce or eliminate offsite storage and warehouse space. We often find companies that have offsite storage for slow-moving or obsolete inventory. However, more times than not, companies “forget about it” because it is out of sight and out of mind. Writing off this inventory may be painful for some, but companies must look at the cost of storing inventory offsite when making these decisions.
-
Consider how conveyors, robotics, or AMRs could be used to reduce travel time for various functions such as putaways and replenishments. Take returns, for instance, inventory that is good to return to stock could be placed on robots, or AMRs, and when full can deliver those goods to a specific zone in the warehouse. This reduces the travel time, but also the delays and distractions workers face when they leave their work areas.
-
Replace aging equipment that has high repair costs and that is constantly out of service. When equipment is down, it creates resource contentions and usually slows down the operations. Get the equipment you need so it can be utilized when you need it, there are very few cases for a company simply living with aging equipment.
-
Determine if you are using too much void fill when packing orders. This can drive up costs but may also mean that you are using too large of a shipping carton – which means shipping “air.” Analyze the items and orders and find the right balance of void fill to not create customer issues or unnecessarily drive-up packing supply costs.
-
Determine if some subset of your shipments could ship in poly bags, if so, auto baggers may be a great way to eliminate labor and packaging costs.
- Determine if outsourcing fulfillment operations or some portion of the tasks can reduce costs. If you are in a high labor cost market, you may find that outsourcing fulfillment could be done at a lower cost. Fulfillment operations and associated functions are frequently outsourced and can lead to increased customer service.
These are just a few ways that companies can utilize and help to lower their labor and fulfillment costs. Each business is unique, and the ideas above must be tailored to your specific operations and goals.
SHARE