Problem:
With the management mantra “do more with less,’ moving into a larger space is not an option; you need to get more throughput and increased capacity out of your current physical layout and facility.
Solution:
Our 18 Industrial Engineering Principles are the best foundation for maximizing throughput and capacity from an existing facility. Use these principles to rethink how you use your fulfillment center and develop the most appropriate solutions for your needs.
With the management mantra “do more with less,’ moving into a larger space is not an option; you need to get more throughput and increased capacity out of your current physical layout and facility.
Solution:
Our 18 Industrial Engineering Principles are the best foundation for maximizing throughput and capacity from an existing facility. Use these principles to rethink how you use your fulfillment center and develop the most appropriate solutions for your needs.
18 Industrial Engineering Principles
- Involve your warehouse staff in decision making relating to facility layout or operations planning. Those people closest to the process usually understand it best. An effective consultant brings experience in many different environments, improve capacity and throughput and can facilitate change.
- Make sure you are utilizing the potential storage space/cube of the warehouse effectively. Insure that vertical space as well as individual location cubic capacity is fully utilized. Maximize cube as well as ground level square feet.
- Focus on slotting, replenishment, and location control system. These three activities form the backbone of the operation and should be given the appropriate attention. If they are cared for, much of the rest of the operation will run effectively.
- Maintain flexibility in the operation and layout. Planning for unknown future changes to the business or fulfillment model is a necessity to avoid unnecessary costs to make unplanned changes to the facility and operation. Don’t develop a layout or process that is inflexible or scalable.
- Minimize congestion and interference with smooth flow. Avoid unnecessary congestion or overcrowding in the warehouse. The time lost due to overcrowding or congestion is significant.
- Reduce cost of fulfillment by simplifying the process. The more times you touch product the higher the cost per order.
- Use a variety of location storage media for slotting and reserve as dictated by item cubic velocity. The one-size-fits-all approach rarely works to maximize efficiency in space and labor performance.
- Minimize travel/walking time. Since more than half of the total labor time you pay for in the warehouse is spent walking, any efforts to reduce travel distance and time will pay off in reduced labor costs. Effective layout and slotting processes can help reduce walking time.
- Use conveyors for horizontal transport of product. Whenever possible, the use of a simple transfer conveyor system can improve operating efficiencies by reducing handlings and walk time. Make sure the cost of the equipment is justified. Conveyor selection is based on the size and weight of he product and the throughput volume. Accumulation has to be planned for in any conveyor design.
- Provide adequate accumulation and storage space on docks. Inefficiencies caused by lack of space on docks gets the operation off to a bad start and not only causes inefficiencies in the operations on the dock but ripples down to and can negatively affect other warehouse functions.
- Cross dock where possible. The ability to omit steps in the fulfillment process and take receipts directly to the packing/shipping function will save time. Consider using cross docking for back order processing as the item is received.
- Keep 10% of locations open and available. This may not be possible 100% of the time, but it is a key factor to have available space to store inventory in picking and reserve locations.
- Move as much product at one time as possible. Maximizing the product per trip will reduce the total trips and time required. Applications can be found in the picking, put away, replenishment, etc. warehouse functions.
- Have a well designed pack station. Since a high percentage of labor is spent in the packing function, it makes sense to insure that all of the required materials are available for the packer and that adequate work space is provided.
- Stagger shift start times. Make sure that your schedule for warehouse staff coincides with work being available. Consider off-shift activities to minimize interference with other warehouse functions.
- Aisle mapping. A simple process that validates that the correct item is in the assigned location will save headaches in other warehouse activities.
- Automation. Provide for the level of automation that can be cost justified based on your particular operation and cost structure. Look for 18-month payback as a guideline.
- Flow charts. Develop a process flow chart that tracks a receipt through the put away process and an order from replenishment to shipping, showing the path and number of times the product is touched.
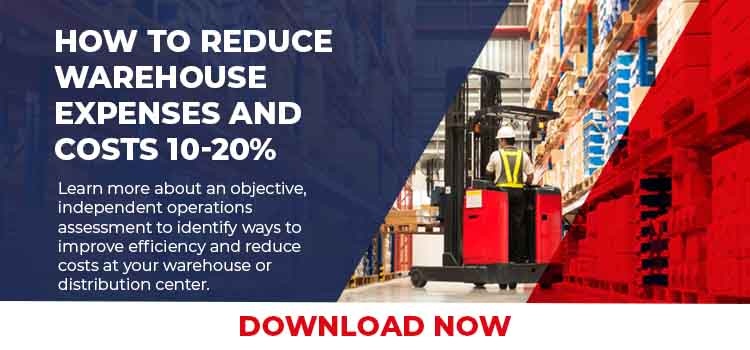
SHARE