Warehouse space planning processes play a role in optimizing warehouse operations and improving efficiency in distribution centers. In today's world, a well-designed, efficient warehouse layout and organization can significantly boost productivity, cut down costs, and enhance workflow.
Having a checklist for warehouse space planning is key for businesses to navigate through this process starting from assessing current storage requirements to predicting future expansion. Important factors like inventory management, material handling equipment, and safety considerations play a role in this assessment.
By addressing these elements, companies can establish well-structured warehouse spaces that cater to existing needs, and future growth. Effective warehouse space planning ensures that every inch of the warehouse is used efficiently. This results in greater operational efficiency and throughput, faster order processing, and increased customer satisfaction.
This systematic approach is essential, for any business looking to improve warehouse operations and stay ahead of the competition.
Defining your company’s warehouse and distribution requirements, along with warehouse equipment, involves a detailed planning process. Not only do you have to accurately plan your current space needs but find a potential facility that meets a high percent of your requirements needed for growth. Consider how each facility will benefit your supply chain.
During the planning phase, the warehouse management team must take into account the following aspects when considering a new facility, or redesign of an existing facility:
- Creating the most efficient layout for the operations long term.
- Creating the most efficient workflows for each warehouse process.
- Eliminating potential safety issues for all workers.
- Maximizing the vertical space for the highest density.
- Utilizing the right type of equipment and automation.
- Adequate space for support functions like maintenance.
- Designing maximum efficiency, inventory flow, and warehouse processes.
If suitable buildings are not available, then a longer-term strategy of build-to-suit (BTS) is necessary. A blank slate with a BTS can be beneficial if your warehouse operations, or warehouse layout designs are so unique.
Regardless of which option (lease, purchase, or BTS), identifying the detailed space requirements is the crucial first step before touring warehouse locations. These requirements can be determined in a disciplined internal warehouse assessment and optimization review.
Here is a 15 point checklist to help you identify your current space use and future growth requirements:
1. Clear Stack Height
The clear stack height is the useable height for storing products, supplies or inventory within pallet racks and shelving. Utilizing as much of the vertical space as possible is critical.
Clear height is measured from the bottom of the facility’s bar joist, lights, sprinkler heads or duct work – to the concrete pad. It is critical to know your max pallet height, the total pallets high you are planning to store, and what the minimum clear height is. This allows you to plan pallet racks and shelving accordingly.
If you select a building that is too low, you will require more square feet of storage. You also must keep in mind local code requirements as most municipalities require at least 18” to 36” of clearance from the sprinkler heads. Optimizing the space for storage and warehouse utilization is critical when building costs are so high.
According to recent industry research, warehouses built in the 1960s average 24 ft. Today’s larger warehouses are now approaching 40 ft high, allowing far more product storage capacity. Warehouses beyond 40 ft require specialized high reach fork trucks and warehouse equipment. Warehouse automation also utilizes this increase vertical space most efficiently.
These types of warehouses all offer something different for each company. As such, they should each be evaluated based on how well they serve your warehouse
2. Total Square Footage
During each step in determining your space needs, it is vital to take into account inventory and order volume growth. The space requirements need to align with the number of years you intend to stay in the facility.
Prevent under sizing the facility by considering the clear height when determining total square foot requirements. Be sure to take into account how much space you need for receiving, staging and inspection of product. If you require a dedicated picking module or pick zone, you will also need to determine the bulk storage in relation to the clear height, as well as picking of inventory.
When planning space needs, don’t stop at determining the current SKU counts. Consider how SKU growth and inventory growth will impact the number of bulk locations and pick bin requirements. Will inventory turns be constant or changing? How will this impact the storage space required?
Consider the type of pallet rack as well. Standard, select pallet rack has a different minimum aisle width and utilization compared to that of push back pallet rack, drive in pallet rack or even pallet flow.
Also, consider space required for packing, shipping and staging for outbound orders. The shipping process will have a significant impact on an efficient warehouse layout design. Wholesale distribution and manufacturing typically requires much larger outbound docks and staging awaiting routing, etc. for LTL and TL shipments. Whereas consumer driven businesses can typically live load small parcel trailers.
Don’t overlook determining the space required for plant or facility maintenance, offices and breakrooms, kitting or other value-added services, conveyors and automation, and returns processing. Be sure to provide ample space for these functions as these will greatly increase the overall square footage.
A warehouse design expert can ensure that you do not undersize the overall facility based on SKUs, inventory and order growth.
3. Dock Doors
This is one area many companies underestimate and always wish they had more of. Consider how many dock doors you need for inbound receiving of goods, consider future growth, and how containers may impact needs. Negatively affecting dock to stock times with too few doors is an operational bottleneck that should be avoided as they affect warehouse efficiency.
On outbound docks, consider what carriers you currently ship with and how that might change in the future. How many different carriers (LTL, TL and small parcel carriers) and how many different sorts are required? Will you have carriers drop trailers throughout the day, impacting the useable doors?
You will also need to make sure you have the right number of doors by type. Most multi-tenant facilities have typical dock height doors and may not offer any ground height doors or ramps. These can be extremely helpful for bringing in large warehouse equipment and other items. Companies receiving or shipping with small parcel carriers using delivery trucks may want to consider doors suited for these trucks.
Lastly, determine if you will utilize doors for compactors and recycling. These two pieces of equipment are large and consume exterior dock space. They will also impact the number of usable doors for the facility. Factor how much trash and recycling will be generated from receiving and returns. These warehouse processes need sufficient space and access to trash and recycling areas. If too space is allocated, this will lead to less than efficient operations.
4. Dock Equipment
For pre-existing facilities, consider what dock equipment you require and the condition of that equipment. Most newer buildings typically come with dock shelters/seals and pit, or hydraulic dock levelers. Dock shelters are important for minimizing hot or cold air from entering the facility as well as dirt, rain, bugs and rodents.
Hydraulic dock levelers are preferred over edge of dock levelers and manual dock plates. They are safer and easier to operate. Check that all dock doors are in good working condition.
The landlord should provide properly functioning levelers and shelters that aren’t worn out. These do require some maintenance and repairs over time but are essential to a well-run facility.
Determine what other dock equipment your company requires and whether the landlord or builder will provide these. You may need dock locks and safety lights to ensure trucks don’t pull away prematurely. Additional needs might also include inside lighting for seeing inside the trailer, as well as safety barricades for empty docks.
5. Electrical Requirements
This is an often-overlooked aspect of a new building. If you have a fleet of lift trucks and stock pickers, you want to ensure the facility has enough capacity to support the charging requirements. Even small to mid-sized facilities can present challenges. Often times, certain warehouse automation and technologies can require 480V 3Phase, but not every facility handles this capacity.
One solution is running new service, which requires permitting and could take several months. A quicker potential solution is asking if your lift truck manufacturer, warehouse equipment manufacturer, or automation integrator offers an alternate power option.
Consider power needs for conveyors, automation, and other equipment needed for manufacturing and light assembly.
6. Building Shape and Footprint
The building’s shape significantly impacts a facility - not all warehouse spaces are created equal. Buildings that are “L” shaped are just as bad as buildings that are long and skinny.
The same is true for inefficient and poorly designed u-shaped layouts. Leased buildings with multiple tenants where expansion is linear creates problems with workflow and travel time. Additionally, warehouse shape can greatly affect pallet racks, often leading to a less than efficient layout.
They disrupt flow and can create additional walking, which adds operational cost. Consider how you will utilize the facility and the overall flow from receipt through outbound.
Understand how other aspects of the building will affect flow, labor costs and productivity. Try to minimize or eliminate offices or any obstructions along the dock. Keep a clear view of the dock (both inbound and outbound) to effectively manage the work and processes.
At times, older manufacturing facilities may have appealing aspects, but may also have overhead cranes, etc. that impact clear height or useable floor space. Some buildings may have structural columns that are very closely spaced, creating issues with pallet rack aisles.
Buildings with odd turns or corridors can end up creating unusable space. Understand how all these facets of a building could negatively impact your operations and warehouse management.
7. Truck Yard
Determine your needs for inbound and outbound staging of trailers. Your needs today could differ vastly in two to three years. Will you have inbound carriers dropping trailers or containers that could impact the number of trailers at the building?
Some companies choose to keep certain supplies like corrugated boxes or merchandise in trailers at peak times so they can drop them at a dock door. Will you have similar processes and, if so, how many trailers will you need over the life of the facility?
For outbound shipping, many companies need drop trailers for handling peak volumes. This may mean keeping empty trailers in a yard to quickly swap at the dock as needed from trailers in the yard.
Many multi-tenant facilities have minimal yard capabilities and could impact flexibility. At times, there is a correlation between the warehouse size and yard size. Though in today's world, developers are maximizing the warehouse size and squeezing yards and parking. This often leads to a less than efficient layout by potentially having to shuttle trailers regularly.
8. Floor Condition
Evaluating floor condition prior to signing a lease is important. As buildings get older and forklift and order picker traffic increases, the floor’s surface may break down. When this occurs, the floor is harder and harder to clean and maintain.
Consider the overall floor condition and how it will impact your operations. For companies with manufacturing equipment, older buildings can pose an issue with floors that aren’t level or have imperfections. Will you require the floor to be resealed before occupying the space?
Floors that have significant damage should be repaired by the landlord prior to occupancy. Constant jarring and impacts will certainly drive up your maintenance and repair costs on lift trucks.
9. Working Environment
For most companies, warehouses are not conditioned spaces. However, sufficient airflow and ventilation is critical. Companies should consider the functions being performed, such as pick zones and assembly, and the working conditions in these spaces.
For companies requiring climate controlled or humidity-controlled space, you may need to outfit a pre-existing facility. It is important to accurately determine the current and long-term needs for the facility.
Most companies struggle with lighting in the warehouse. They develop a pallet rack design that unfortunately requires the moving of existing lighting. In addition, the lighting must be sufficient to read pick documents and racking labels. High efficiency LED fixtures and providing sufficient lighting can have an ROI within 18 to 24 months based on energy savings.
10. Safety and Fire Suppression
Understand your product classification and your storage requirements as these will have an impact on fire suppression. Companies will need to make sure that a pre-existing facility has the properly sized pumps, sprinkler heads, water flow, etc. to handle your inventory.
If your product classification or insurance carrier require in-rack sprinklers, this can present challenges. Unless the building already supported in-rack sprinklers, there is a higher likelihood that the existing sprinkler system will not support this requirement.
In this instance, there may need to be new pumps, additional piping and heads once the pallet rack is installed. This will also require a fair amount of work with engineering and permitting before the work can begin. This will greatly increase the cost to move into a new facility.
Lastly, if there is a need for in-rack sprinklers there may not be sufficient water volume. This can be a real concern for rural areas. In these instances, supplemental water supplies would be required - further driving up the costs. A local fire consultant can apprise you of any safety issues and safety regulations.
11. Employee and Visitor Parking
Developers are typically looking to maximize the total amount of useable square feet. This often means that employee and visitor parking is sacrificed - along with truck yards and trailer staging.
Determine how many parking spots you need currently and through the life expectancy of the building. Are you a multi-shift operation with overlapping shifts? If so, how will this impact the number of spaces required?
Additionally, consider what percent of your employees will be using public transportation, and how far away is access to public transportation.
12. Breakrooms, Bathrooms, and Lockers
You will need to provide sufficient employee facilities including storage of personal items and breakrooms. Determine your needs based on the number of employees and temp workers at peak.
This is one of the more expensive costs from a tenant improvement perspective. It's not uncommon for bathrooms and breakrooms to be undersized if you have larger staff requirements.
Determine what is needed for the following spaces:
- Employees with dedicated offices, like the warehouse manager.
- Small and larger conference rooms.
- Employee training spaces, if different from using conference rooms.
- On the floor workstations.
- Employee lockers and personal storage.
- Space for handheld charging, records management, office supplies, etc.
13. Transportation Access
Consider the volume of truck deliveries per day and how easy is the ingress and egress to the property. If access to the facility is tight, or problematic, this could lead to damaged trailers or to the property. In the case of a leased facility, this will be your responsibility.
Additionally, you should consider the ease of access to major highways and interstates. The same needs to be considered for ports and rail access.
14. Building Expansion
Once you have determined what your space needs are, look at the building in terms of building expansion. Is there sufficient acreage for expansion, parking, and truck transportation? Was the building designed in terms of “knock out” walls and docks? Will you have first right of refusal for adjoining warehouse space?
What are the possibilities for additional dock doors? Understand how mezzanines can add storage and throughput capacity to warehouses as an option.
15. Make an Action Plan for Building Evaluation
With all of these details, itemize the requirements by year for the time horizon the building needs last, for all department areas:
- receiving dock size, staging for checking, marking, quality assurance
- auxiliary functions (e.g. kitting, personalization)
- storage space for product
- packing stations
- common areas for aisles
- employee areas
- returns processing
- shipping dock sizes.
From these detailed space requirements, develop a spreadsheet to allow a succinct side-by-side comparison of each facility and how well each facility meets your requirements. These are critical steps to take long before you begin to think about a warehouse move plan.
Moving fulfillment into a new facility is a major investment and expense to companies. Many times, teams end up under-sizing the new facility and companies run out of space faster than expected. Following these planning steps will help you improve space planning accuracy.
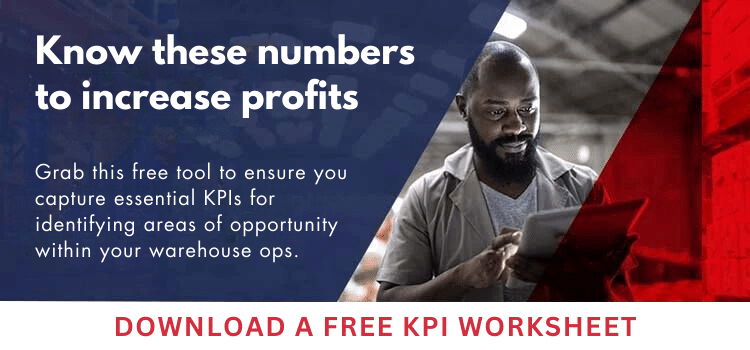
SHARE